Ubicada en Kawachi, en la prefectura de Tochigi, la planta de Nissan cuenta con una larga historia de producción de los vehículos más prestigiosos de la compañía, por ejemplo: Nissan GT-R y Nissan Z. Como la primera fábrica inteligente de la marca, presenta un sistema de producción más cómodo y centrado en la tecnología que está a la vanguardia de la fabricación de vehículos. Recientemente esta planta anunció que ha experimentado una gran transformación: los cambios en la línea de fundición han sido especialmente marcados, por ejemplo, ahora es una línea en la que el 20% del personal son mujeres.
Nissan tiene como objetivo proteger tanto el medio ambiente como a sus colaboradores, esta es la consideración principal en sus instalaciones de producción, con la finalidad de crear un espacio de trabajo lo más cómodo posible. A medida que la marca continúa transformando sus vehículos y tecnologías, da pasos cada vez más grandes para asegurarse de hacer lo mismo en sus plantas de manufactura, lo que es necesario para transformar cada línea de producción y proceso hacia un futuro sostenible.
La división de fundición cubre aproximadamente una cuarta parte de toda la planta de Tochigi, es ahí donde se opera todo el proceso de fundición, como la fusión y el moldeado de metales como el aluminio y el hierro en las piezas del motor. En cualquier fábrica, los procesos de fundición y moldeado son unos de los más exigentes, por lo que requieren un cuidado especial para garantizar que su impacto ambiental sea mínimo. Para Nissan, esta es un área de especial interés.
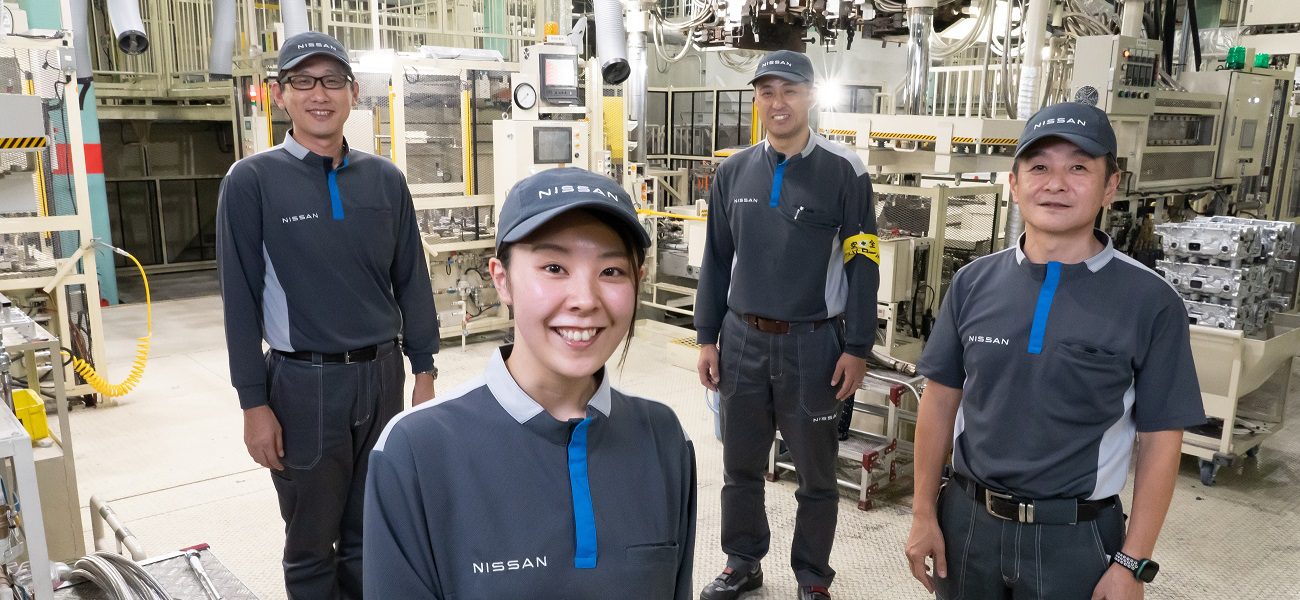
Shinichi Tsuchiya, diseñador de líneas de fundición en la planta de Tochigi, explica: “Cuando comenzó el proyecto de renovación de la línea de la fábrica en 2018, trabajamos para hacer que esta fuera amigable con el medio ambiente y abierta a todos, independientemente de la edad y el género, incluyendo a aquellos que tienen dificultades para realizar trabajos pesados”.
Alcanzar este objetivo requirió una revisión completa, incluida la introducción de los equipos más recientes y avanzados. Esto permitió que el departamento de fundición se volviera más amigable con el medio ambiente y más seguro para las personas.
Al poner un pie en la nueva fábrica, los visitantes notan inmediatamente los pisos de colores brillantes y los espacios de trabajo bien iluminados, que utilizan luz LED ecológica. El aire y el entorno general dentro de la gran instalación de producción se mantienen limpios gracias a los núcleos inorgánicos en los procesos de fundición y moldeo.
Los núcleos inorgánicos que se utilizan contienen un adhesivo llamado vidrio soluble. Cuando se derrite, esta sustancia no genera gases u olores desagradables, eliminando la necesidad de equipos de desodorización.
Además, se realizaron mejoras significativas en lo que respecta a reducir el esfuerzo físico de los colaboradores. En el pasado, se transportaba aluminio fundido desde la fundición hasta la línea de fundición mediante montacargas; sin embargo, al acercar el horno de fusión a las máquinas de fundición, ya no es necesario transportar el metal fundido; de la misma manera, fue reducido el consumo de energía al derretir solo la cantidad necesaria, lo que hace que el proceso sea mucho más eficiente en general.
Inclusive, se ha simplificado enormemente el proceso de inspección posterior a la fundición. Actualmente se utiliza la tomografía computarizada para una evaluación interna mucho más rápida y eficiente, esto reduce en gran medida la carga de trabajo involucrada en el proceso, incluida la carga física.
Reducir el impacto medioambiental general de las fábricas sigue siendo una meta importante. Nissan logró ese objetivo con una reducción del 40% en todo el proceso de calentamiento. “La planta de Tochigi tiene la capacidad de abordar problemas en todas las divisiones y procesos”, declaró el ingeniero de fundición Yosuke Nagamori. “La sólida ética del equipo ha contribuido enormemente a esta mejora”, añadió.
Kana Tsugawa, una colaboradora de la línea de fundición, comentó: “La fábrica es más brillante y el trabajo es físicamente más fácil”. Con la reducción de las emisiones de gases, Kana agrega que el equipo ahora puede socializar después del trabajo sin necesidad de ir a casa a cambiarse. Nissan se ha fijado el objetivo de lograr la neutralidad de carbono durante todo el ciclo de vida del vehículo para el 2050. La introducción de Nissan Intelligent Factory en la planta de Tochigi es un pilar importante de esta iniciativa. La compañía está impulsando innovaciones de este tipo para mejorar la eficiencia productiva en el montaje de vehículos, tanto en términos de energía como de materiales.